- ホーム
- グループについて
- NISSHIN Stories
- 冷凍食品のパッケージサイズ変更で、ドライバーの作業負荷を削減!!“2024年問題”にも対応するイノベーションはなぜ生まれたのか
冷凍食品のパッケージサイズ変更で、
ドライバーの作業負荷を削減!!
“2024年問題”にも対応するイノベーションはなぜ生まれたのか
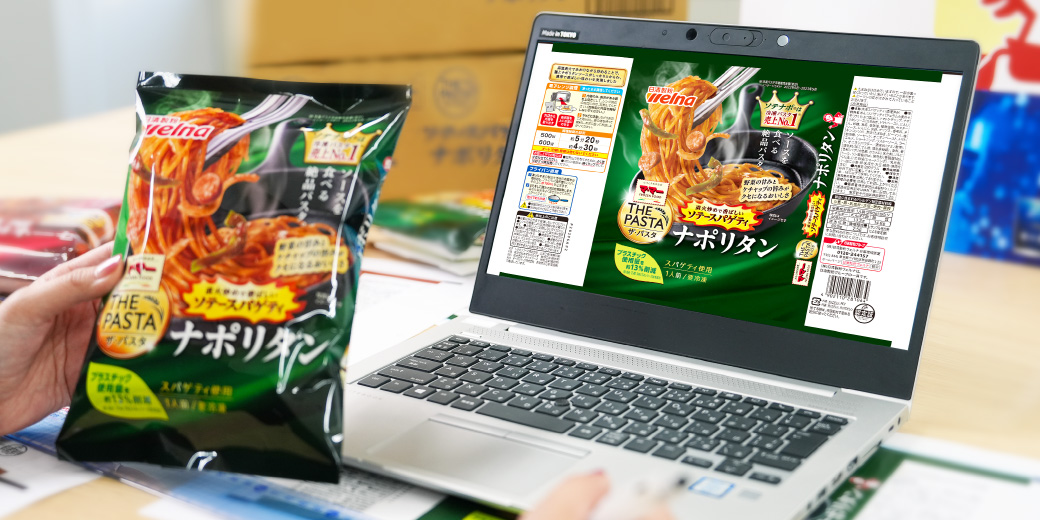
日清製粉ウェルナは、冷凍食品の輸送では普及していなかったパレット活用による積載効率化を目的に、計200品にも及ぶ冷凍食品のパッケージサイズの変更を2023年8月から順次開始した。これによって製品の積載効率は約1.5倍向上※し、ドライバーの積み下ろしの作業時間も大幅に短縮される。その先に目指すのは、冷凍食品業界全体での共通パレットを使うことによる輸送効率の抜本的な改善だが、今回の取組みは、そこに向けた大きな一歩となった。このイノベーションが、どのようにして生まれたのかを、担当者が明かす。
※1パレット当たり
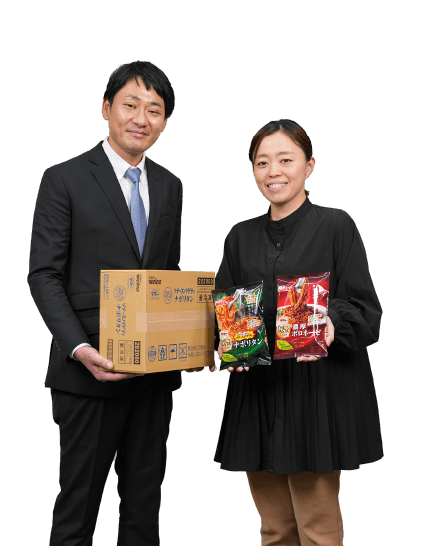
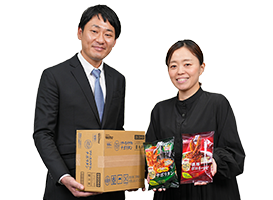
PROFILE
株式会社日清製粉ウェルナ
プロダクトマネジメント統括部 第三部生産第一グループ チームリーダー
見澤 誠司(左)
2007年入社。冷凍食品事業(主に生産・品質管理)を約10年経験した後、2018年よりタイ日清製粉の冷食工場製造部長を務める。2022年より現部署にて冷食の生産管理を担当。
プロダクトマネジメント統括部 第三部ディレクショングループ 家庭用担当チームリーダー
鈴木 智恵(右)
2008年入社。業務用営業部にて外食向けの営業として卸店や大手ユーザーを担当。2015年より家庭用冷食の広告宣伝業務に従事。2021年より現部署にて商品開発を担当。
所属・役職は取材当時
冷凍食品業界に横たわる
「物流課題」と「2024年問題」
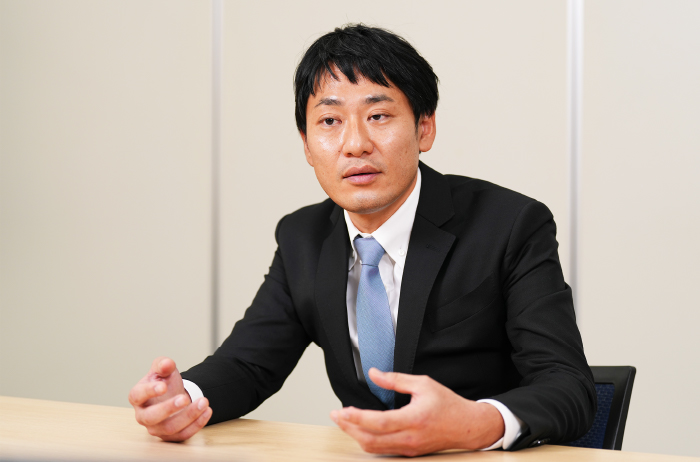
「実は冷凍食品業界では、常温の製品とは違う、ある商慣習が根付いているんです」
そう話すのが、今回のプロジェクトを生産面でリードした、プロダクトマネジメント統括部 第三部生産第一グループ チームリーダーの見澤さんだ。
「段ボールの大きさが不揃いな冷凍食品業界では、バラ積みが基本となっています。トラックへの積み下ろしはパレットごとではなく手作業で行うため 、段ボール(ケース)を積むにも下ろすにもそれぞれ2時間程度かかり、輸送効率の面で課題を抱えていました」
さらには、そこに“2024年問題”ももちあがった。2024年問題とは、トラックドライバーの年間の時間外労働時間が法令で制限されること等に伴う、物流業界全体にかかる諸問題だ。マーケティング面のリード役を担った、プロダクトマネジメント統括部 第三部ディレクショングループ 家庭用担当 チームリーダー 鈴木さんは、こう語る。
「そうした背景から、冷凍食品の輸送にもパレットを活用することが急務になりました。それには、効率的にパレットへ積むために冷凍食品の段ボールサイズを見直す必要があり、そのために製品のパッケージサイズ自体の変更が必要になったんです」
イノベーションは、試行と改善の積み重ねで生まれた
パッケージサイズ変更の対象となった冷凍食品は、家庭用・業務用をあわせて計200製品に及んだ。
「共通設備を使用するので、『一部の製品だけを仕様変更する』ということができず、すべての製品で成立しなければなりませんでした。また、設備は改造すると後戻りはできないため、さまざまな検証を重ね、全7工場の設備を変え、製品仕様を確定することになりました」(見澤さん)
製品仕様の確定にあたっては、まず日清製粉グループ本社 生産技術研究所が、容器包装技術と専門的な知見をもとに、容積縮小の基本的な手法を検討した。その提案内容をもとに、日清製粉ウェルナの生産グループで実際の製造ラインへの適性や厚みの微妙な変化による調理解凍性など品質への影響について検証し、製品仕様を確定。その後、マーケティンググループが、包材メーカーはもちろん、社内の営業部・お客様相談室・品質管理グループ・購買課等と調整・連携を行った。
「特にこだわったのが、内容量、調理時間を変えないことです。今回のサイズ変更は、あくまで物流課題の解決が目的であり、そのためにお客様の経験価値を損ねてしまっては絶対にならないと考えました。ただ、それらを変えずに最適なサイズを見出すことは、至難でした。」(鈴木さん)
製品サイズを変えるには、凍結用トレーから製品搬送設備、包装機までを見直す必要があり、それをミリ単位で試行錯誤していった。
「同じ規格の段ボールであっても、実際は数ミリの誤差や個体差があります。また、検討によって見出した最適なサイズでも、実際に工場に落とし込む段階でうまくはまらず、仕様を急遽変えることもありました。結果的に『実地でやっては、改善する』というプロセスをひたすら繰り返す形となりました」(見澤さん)
そうしたサイズ設計に関する壮大な試みと並行して、マーケティンググループでも試行錯誤のもと、準備が急ピッチで進められた。
「PB(プライベートブランド)のお客様に対する説明・調整や、お客様相談室用の資料の作成、品質保証のサポート等を一気に実施していかなくてはなりませんでした。というのも、プロジェクトが本格的に動き出してから実質半年ほどでプレス発表までこぎつける必要があったのです。この期間でこれだけの商品を改版するというのは異例のことでした」(鈴木さん)
製品と段ボールのサイズ見直しとその効果
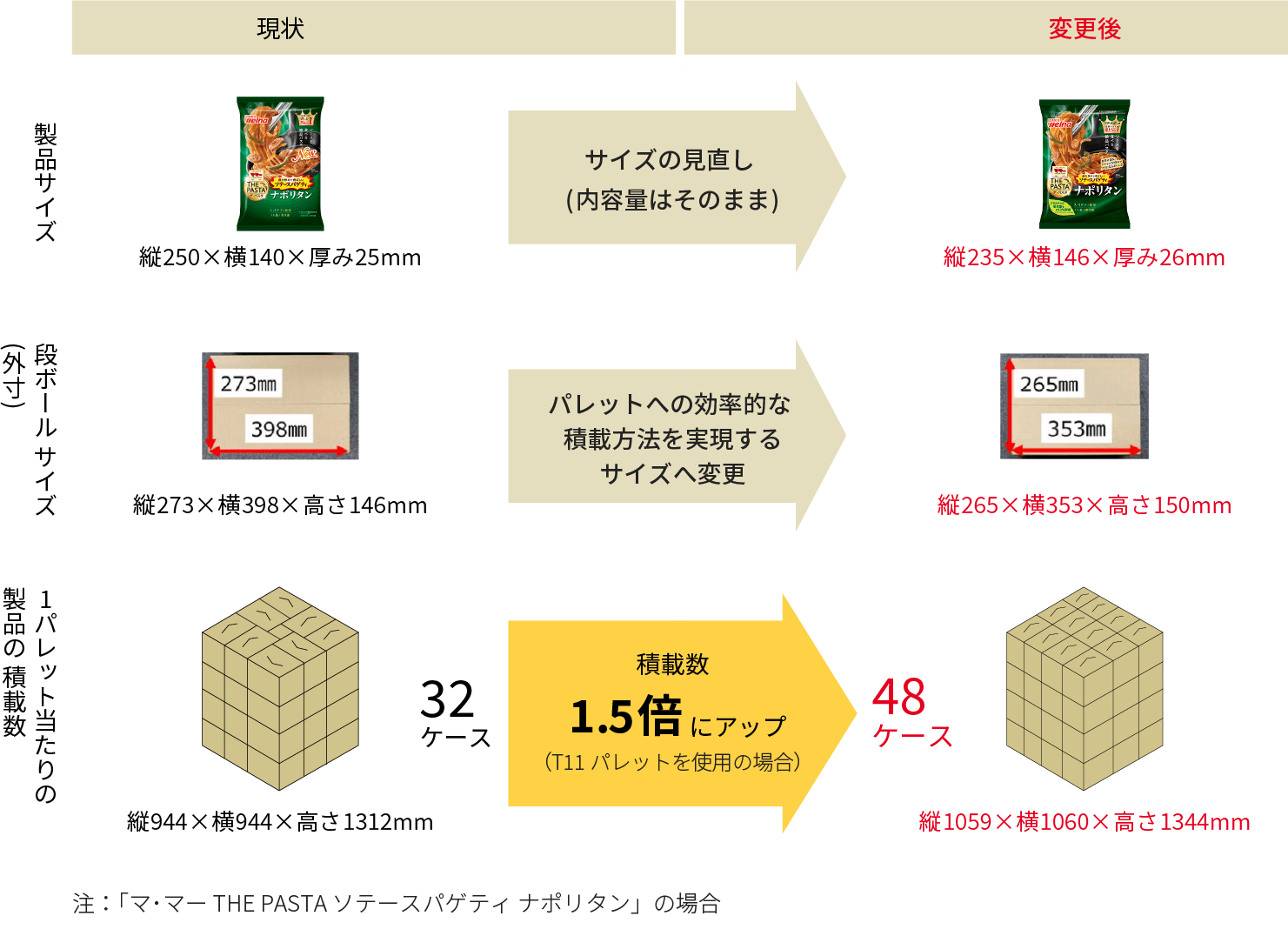

いざ取り組んでみたら、
サプライチェーン全体にメリットが
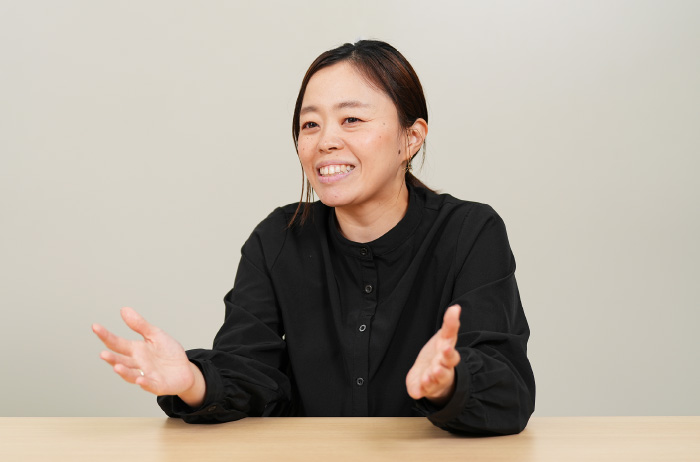
こうした取組みの末、ついに計200品のパッケージサイズ変更の目処がついた。それによって実現したのが、冒頭でも紹介した「輸送効率の大幅な改善」だ。1パレット当たりの製品の積載数は、パッケージ変更前の約1.5倍に向上。また、パレットを使うことで、積み下ろしに計4時間ほどかかっていたドライバーの作業時間は、半分以下で済むようになる見込みである。
さらに、当初の目的はパレットの積載効率を上げることだったものの、結果的には他のさまざまな“副産物”も生まれた。
「例えば今まで複数あった凍結トレーや包装資材等も見直したことで集約ができ、製品アイテム毎での切替作業も不要になり、製造効率が上がり、製造の安定化にもつながりました。今回、改めて製品一つひとつと向き合ったことで、多くの改善の余地に気づかされたんです。工場や資材メーカーの負荷も下がりますので、サプライチェーンを通して見れば一石二鳥どころか三鳥、四鳥もの効果が生まれました」(見澤さん)
「今回の変更では、製品の外装包材の厚さも0.01mm薄くしました。それによりプラスチック使用量を約13%削減※1できた上、1ロール1000mの包材を保管するスペースも縮小でき、重量も軽量化されたため、ロール交換の負担も軽減できました。」(鈴木さん)
また、取組みをプレス発表したところ、他の冷凍食品メーカーやメディア等から多くの問い合わせが入った。
「今回のプロジェクトで、こうした社会課題の解決につながる取組みが、大きな反響を呼ぶことを実感しました。一方、冷凍食品の輸送課題は、冷凍食品業界全体で共通パレットを使うことによってこそ抜本的な解決に至ります。当社は『F-LINEプロジェクト』※2にも参画しており、今後も他の食品メーカー様とも連携しながら、物流問題の解決へ意欲的に取り組んでまいります」(鈴木さん)
※1 当社「マ・マー THE PASTA」シリーズ従来品比
※2 食品物流の諸課題に対して食品メーカーが協働で検討する2015年発足のプラットフォーム。物流企業のF-LINE株式会社と、合計6社の食品メーカーが参画する。 参画メーカーは、味の素株式会社、カゴメ株式会社、日清オイリオグループ株式会社、株式会社日清製粉ウェルナ、ハウス食品グループ本社株式会社、株式会社Mizkan(五十音順)